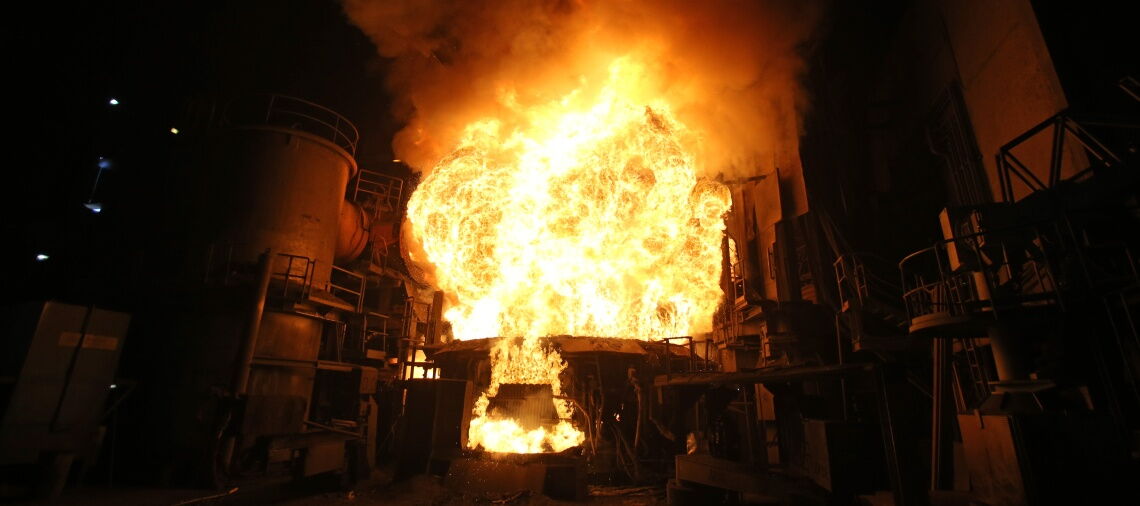
Picture-Alliance/dpa
Stahlproduktion in einem Lichtbogenofen: Die Branche muss ihre Prozesse umstellen, um klimaneutral zu werden.
Von Kathinka Burkhardt
Wenn es nicht gelingt, das CO2-Problem der Stahlindustrie zu lösen, wird die Welt die Zusagen des Pariser Klimagipfels verfehlen. Jede zehnte Tonne CO2, die irgendwo auf dem Globus freigesetzt wird, geht auf die Stahlbranche zurück. Denn Stahl ist ein Alleskönner, stabil, formbar und günstig, der in unzähligen Bereichen zum Einsatz kommt – auf dem Bau und in Autos genauso wie in Pipelines und Windrädern.
Das Problem ist die Art, wie rund drei Viertel des weltweiten Stahls hergestellt werden. Der Grundstoff dafür ist reines Eisen, das man gewinnt, indem man Eisenerz in Hochöfen auf etwa 1700 Grad erhitzt. Dabei wird auf zwei Arten CO2 frei: Zum einen stammt es aus dem Brennstoff der Hochöfen, in der Regel also aus Kokskohle. Zum anderen entsteht in einer chemischen Reaktion im Hochofen Gichtgas, das wiederum viel CO2 enthält. Beides zusammen führt dazu, dass die Stahlwirtschaft in Deutschland für rund ein Viertel aller Emissionen der Industrie verantwortlich ist.
Grüner Wasserstoff soll Kokskohle ersetzen – und den Stahl vom CO2 befreien
Doch es gibt auch eine andere, saubere Art, das für die Stahlproduktion nötige Eisen zu gewinnen: mit grünem Wasserstoff. Das geruchlose Gas reagiert dabei mit Eisenerz und entzieht diesem Sauerstoff. Chemiker nennen das eine Reduktion; die Anlage, in der dieser Prozess stattfindet, heißt Direktreduktionsanlage. Zurück bleibt Eisenschwamm, der in einem Lichtbogenofen geschmolzen zu Rohstahl verarbeitet wird. Stammt der dafür nötige Strom aus erneuerbaren Quellen, ist der Stahl CO2-frei.