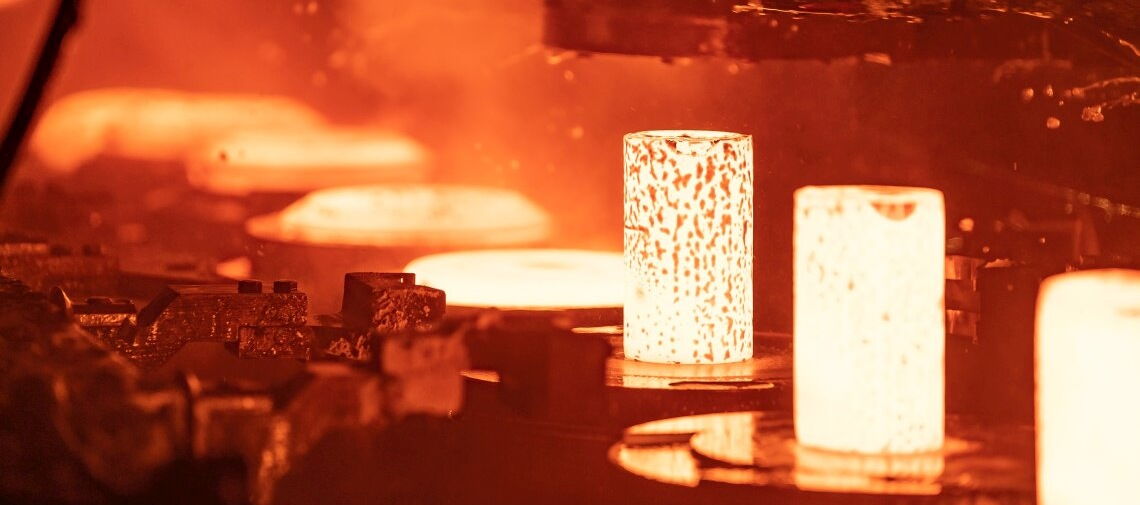
Fokussiert Fotografie
200 Tonnen Rohstahl verarbeitet Neumayer für Autohersteller und andere Abnehmer – jeden Tag. Der Energiebedarf ist gewaltig.
Von Daniela Schröder
In der Fabrik ist es laut und dämmrig, aus wuchtigen Öfen rollen rotglühende Stahlteile. Draußen liegt Schnee auf den Hügeln und Bergen, drinnen schwitzen die Arbeiter in ihren T-Shirts. Stahl, mehr als 1100 Grad heiß, darum dreht sich alles bei der Richard Neumayer GmbH. Am Firmensitz in Hausach, einem beschaulichen Schwarzwald-Städtchen, entwickelt und fertigt das Familienunternehmen Schmiedeteile und Komponenten für die Autoindustrie und den Maschinen- und Anlagenbau: Zahnräder, Bremshebel, Kolben, Bauteile für Motoren, Getriebe, Fahrwerke. Jeden Tag gehen bis zu 200 Tonnen Rohstahl in die Fabrik rein und als fertige Teile wieder raus.
Früher wurden die glühend heißen Stahlteile nach dem Umformen abgekühlt und später mit Erdgas für den nächsten Schritt erneut erhitzt. Vor einigen Jahren stellte Neumayer auf Wärmerückgewinnung um: Die heißen Teile kommen jetzt in einen riesigen Behälter, ausgekleidet mit wärmespeicherndem Schamottstein. Die eigene Hitze hält sie dort über Stunden auf einer gewissen Temperatur, bevor sie in die nächste Stufe der Produktion gehen.
„Durch das Nutzen der Wärme sparen wir nicht nur den Arbeitsgang des Wiedererhitzens der Schmiedeteile“, sagt Unternehmenschef Dirk Neumayer. „Vor allem sparen wir eine Menge Energie, denn das Wärmeverfahren braucht 95 Prozent weniger Erdgas. Für uns bedeutet es deutlich geringere Kosten, zugleich senken wir unseren CO2-Ausstoß um mehrere Tausend Tonnen pro Jahr und tragen so wirksam zum Klimaschutz bei.“