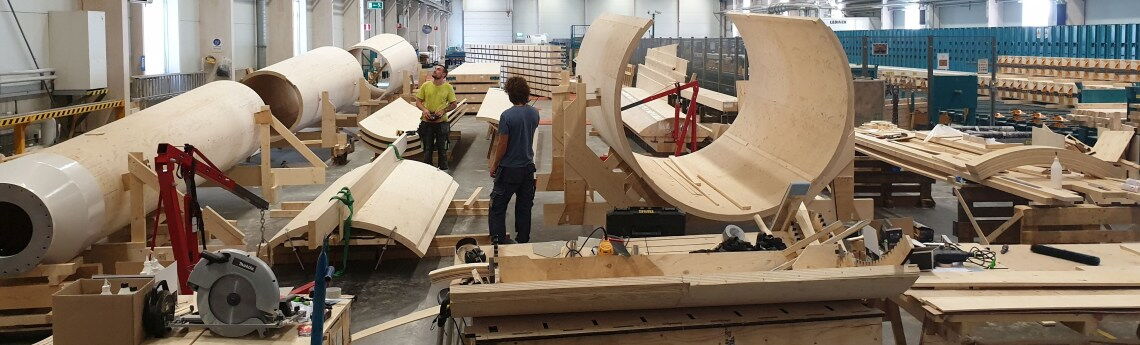
Modvion
Bau eines Holzwindrads in Schweden: Analysten bescheinigen dem Material viel Potenzial.
Nachhaltig produzierte Windräder
Modvion
Bau eines Holzwindrads in Schweden: Analysten bescheinigen dem Material viel Potenzial.
Von Denis Dilba
Höher, größer, stärker, das ist das Gesetz der Windenergie. Mit ihren imposanten Anlagen bricht die Branche einen Rekord nach dem anderen, 2020 lieferte sie bereits 26 Prozent des deutschen Stroms. Doch die Größenjagd bringt auch Nachteile mit sich, gerade an Land: Höhere Windräder mit längeren Flügeln erzeugen stärkere Geräusche und benötigen mehr Fläche. Zudem verbrauchen die Bauteile wachsende Mengen Stahl und Beton, deren Produktion CO2 verursacht. Hinzu kommen Transportprobleme – schon heute passen die Bauteile kaum durch Tunnel und werden zu schwer für Brücken.
Probleme, die aus Sicht von Professor Torsten Faber nicht sein müssen. Der Leiter des Wind Energy Technology Institute (WETI) an der Hochschule Flensburg hat mit seinen Studenten ein Alternativkonzept entwickelt. Ihr Windrad mit den Namen Optimus LE hat einen 80 Meter hohen Turm und bringt es mit einem Rotordurchmesser von 92 Metern auf zwei Megawatt. Das ist bescheiden im Vergleich zu den 15-Megawatt-Anlagen mit 150-Meter-Turm und 220 Metern Rotordurchmesser, die auf See geplant werden. Doch die eigentliche Besonderheit besteht im Material: Optimus LE ist nahezu vollständig aus Holz.
„LE steht für Low Emission“, sagt Rasmus Dohnke, aktuell Leiter des Holzwindradprojekts im Masterstudiengang Wind Energy Engineering. „Zum einen sind unsere Holzrotoren etwas kürzer als die von Anlagen in ähnlicher Größenklasse, was sie laut unseren Simulationen rund sechs Dezibel leiser macht. Zum anderen ist auch die Höhe des Holzturms geringer. Damit ist Optimus LE weniger weit sichtbar und reduziert sozusagen die optische Emission.“
Obendrein macht das nachhaltige Baumaterial die Anlage klimaneutral. „Holz verursacht keine CO2-Emissionen bei der Produktion, im Gegenteil es speichert das Treibhausgas sogar“, sagt WETI-Leiter Faber.
Auch nach dem Ende seiner Lebensdauer habe ein Holzwindrad Vorteile: Das Material sei zu 100 Prozent recycelbar und setzte selbst bei der Verbrennung kaum zusätzliches CO2 frei, sagt Faber. Ganz anders als die üblicherweise aus dem Verbundwerkstoff GFK mit hohen CO2-Emissionen hergestellten Rotorblätter, die beim Verbrennen giftige Gase freisetzen würden.
Unter anderem deswegen sei er auf die Idee gekommen, seine Studenten ein Windrad aus Holz konstruieren zu lassen. Das Projekt, an dem aktuell 17 Studenten aus neun Ländern arbeiten, geht gerade in sein zweites Jahr. „Der Turm ist noch der von unseren Vorgängern“, sagt Projektleiter Dohnke. „Die Rotoren, die Verkleidung der Generatortechnik und den Spinner, der die Nabe umhüllt und möglichst aerodynamisch gestaltet ist, haben wir neu entwickelt“, sagt der 26-Jährige.
In Zweierteams widmen sich die WETI-Studenten Teilaufgaben wie der Generatorkühlung oder dem System zur Steuerung der Anstellwinkel der Rotoren zum Wind. Das Rotoren-Team hat eine der anspruchsvollsten Aufgaben, dafür aber auch Unterstützung von einem Pionier der Szene: Gregor Prass, einst Kopf der Firma TimberTower, berät die Studenten. „Ich halte Kontakt und beantworte Fragen, wo ich kann“, sagt Prass. Er war maßgeblich für den Bau des ersten Windrads mit Holzturm 2012 in Hannover verantwortlich. Als einer der wenigen weltweit hat der 48-jährige Bauingenieur zudem Erfahrung mit der Fertigung von Holzrotoren.
Doch sowohl das Rotoren-Unternehmen, an dem Prass beteiligt war, als auch TimberTower haben den Durchbruch nicht geschafft. Das habe verschiedene Gründe, sagt Prass, „insbesondere den, dass Banken, Versicherungen und Investoren beim Thema Klebetechnik für Holz aus Unkenntnis heraus Angst haben.“
An Problemen mit dem Naturwerkstoff selbst liege es aber keinesfalls, versichert Prass. Der 100 Meter hohe TimberTower-Prototyp mit 1,5-Megawatt-Generator im Hannoveraner Stadtteil Marienwerder liefert noch immer verlässlich Strom. Zu weiteren Projekten kam es dennoch nicht: Prass verließ das Unternehmen 2015 nach Differenzen mit einem neuen Hauptinvestor. Mit ihm ging auch das Know-how, die Geschäfte schliefen ein.
Prass entwickelte die Holzturmtechnik aber später weiter. Beim Prototyp hatte er mit einer achteckigen Grundfläche und Brettsperrholzplatten gearbeitet, die er nun durch leistungsfähigere Furnierschichtholzplatten ersetzte. Dann entwickelte er eine Turmvariante, bei der auf der Baustelle nicht mehr geklebt werden müsse.
„Der Schlüssel dazu ist eine neuartige Form der Verbindungstechnik“, sagt Prass. Er hat jüngst ein Unternehmen gegründet, das auf dieser Technologie fuße. Derzeit plant er den Bau von fünf Windrädern in einem Waldgebiet in Hessen. Dafür hat er sich mit einem Mann zusammengetan, der um die Jahrtausendwende zu den schillerndsten Protagonisten am Neuen Markt gehörte: Tan Siekmann, bekannt durch den raketenhaften Aufstieg und den jähen Absturz der IT-Sicherheitsfirma Biodata.
Siekmann, inzwischen ein Seriengründer, engagiert sich schon länger in der Windkraft. Er erweiterte die Turmvariante von Prass in einem wichtigen Punkt: Bei den fünf geplanten Türmen handele es sich um eine Holzhybridvariante, sagt Siekmann im Gespräch mit EnergieWinde. „Die ersten 100 Meter der 160-Meter-Türme mit Sechs-Megawatt-Generatoren werden aus Holz bestehen, der Rest aus Stahl.“ Das bringe gewissen Zeit- und damit auch Kostenvorteile mit sich.
Infografik: Andreas Mohrmann
Auf dem Meer erzeugen Windräder Strom im zweistelligen Megawattbereich. Anlagen aus Holz sind für den Einsaz an Land bestimmt – und werden kleiner sein.
Laut Siekmann hat die Hybridkonstruktion einen Vorteil: Der obere Stahlturm habe einen so geringen Durchmesser, dass er problemlos transportiert werden könne. Mit Kosten von 150.000 bis 160.000 Euro sei er zudem deutlich günstiger als ein kompletter Stahlturm. „Noch entscheidender ist aber, dass wir teure Großkran-Tage einsparen“, sagt Siekmann. Das Spezialgerät müsse erst zum Aufsetzen der Stahlsegmente kommen, die unteren 100 Meter aus Holz könne man ohne Großkran bauen. „Daher kann er am gleichen Tag auch noch zur Installation von Nabe, Gondel oder Rotoren eingesetzt werden“, sagt Siekmann. Bei Tagespreisen von rund 50.000 Euro für solche Kräne kämen schnell sechsstellige Einsparungen zusammen.
Prass ist sich daher sicher, dass die Zeit der Holztürme nun gekommen ist. „In Sachen Transport, Logistik, Preis und beim CO2-Fußabdruck war der Holzturm schon immer besser als Stahl- und Beton-Konstruktionen“, sagt Prass. „Nur war er bisher nicht etabliert.“
„Unsere neuen Holzhybridtürme werden aus rein kommerziellen Gründen gebaut“, meint Prass. „Wenn da erstmal zehn stehen und alle sehen, dass es perspektivisch auch günstiger ist – wer baut da noch mit Stahl oder Beton?“ Aus solchen Worten spricht natürlich der Verkäufer. Allerdings steht er mit seinem Glauben an die Holztechnologie nicht allein. Andere Unternehmen verfolgen ähnliche Pläne. Modvion aus Schweden hat etwa bereits einen kleinen 30-Meter-Holzturm zu Forschungszwecken aufgestellt und will ab 2022 Holztürme für große Windkraftanlagen bauen. Vorverträge mit Energieunternehmen wie Vattenfall sind nach Angaben des Unternehmens bereits abgeschlossen.
Und auch die Marktforscher von BloombergNEF bescheinigen der Holztechnologie mit Blick auf die Klimabilanz durchaus Potenzial. „Stahltürme müssen sich anpassen, wenn sie weiterhin die erste Wahl bleiben wollen“, erklärte Windenergie-Analyst Imogen Brown.
Ein Hindernis für die Technologie sieht BloombergNEF allerdings in der fehlenden Praxiserfahrung und der nicht etablierten Lieferkette. Prass und Siekmann wollen das nun ändern. „Wenn alles gut läuft, beginnen wir im nächsten Jahr mit dem Bau“, sagt Siekmann. „Die Holztürme sind dabei nur der erste Schritt“, sagt Prass, „wir arbeiten auch schon an Holzrotoren und danach folgen dann hoffentlich auch Fundamente aus Holz.“
WETI-Professor Faber ist insbesondere bei Rotorblättern aus Holz noch zurückhaltender. „Die Fertigungstechnik dafür muss noch verbessert werden. Wir haben dazu schon Ideen entwickelt, die mit CNC-Fräsen arbeiten.“ Trotzdem rechnet der Experte frühestens in fünf Jahren mit ersten in Kleinserien gefertigten Holzrotorblättern.
„Langfristig sprechen aber immer mehr Aspekte für Holz als Baustoff bei Windkraftanlagen“, sagt Faber. Auch hinsichtlich der Haltbarkeit. „Holztürme und Holzrotorblätter aus Schichtholz erreichen locker eine übliche Anlagenlebensdauer von 20 Jahren und mehr“, so der WETI-Leiter. Daher sieht er gute Chancen dafür, dass Optimus LE in Zukunft umgesetzt wird. Darauf hofft auch Rasmus Dohnke. „Da würde sicherlich jemand aus unserem Studententeam beruflich beteiligt sein. Mehr Erfahrung mit der Anlage bringt niemand mit.“