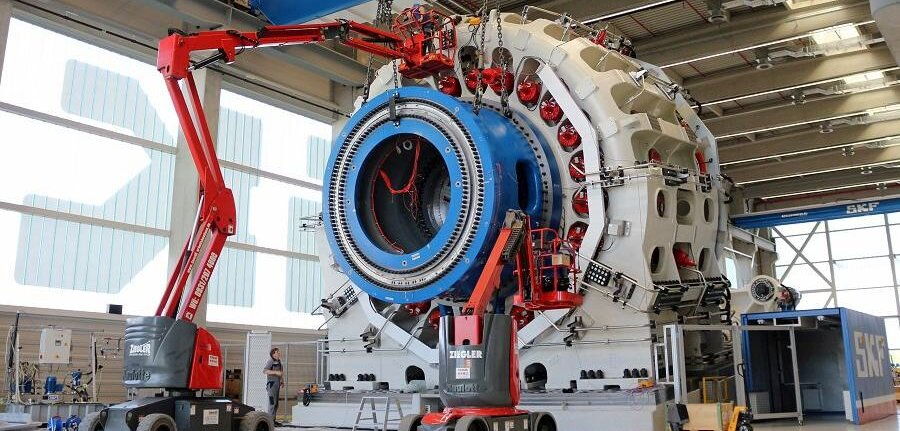
SKF
Prüfzentrum von SKF in Schweinfurt: Jeder achte Beschäftigte in der Offshore-Windkraft arbeitet in Bayern oder Baden-Württemberg.
Bayerische Zulieferer
SKF
Prüfzentrum von SKF in Schweinfurt: Jeder achte Beschäftigte in der Offshore-Windkraft arbeitet in Bayern oder Baden-Württemberg.
Von Steffi Sammet
In seiner Art ist es einzigartig: das Sven Wingquist Test Center in Schweinfurt. In dem leistungsfähigsten Großlagerprüfzentrum der Welt will die SKF Gruppe künftig technologische Pionierarbeit leisten. Der Spezialist für Wälzlager, Dichtungen, Schmiersysteme und Zustandsüberwachungstechnik rüstet mehr als 40 Industriezweige mit seinen Produkten aus – unter anderem die Windkraft.
Weil es bis dato nirgendwo auf der Welt ein Simulationsprogramm gibt, das alle Prozesse im praktischen Betrieb von Großlagern realitätsgetreu abbildet, hat der Konzern aus Unterfranken rund 40 Millionen Euro in ein entsprechendes Prüfzentrum investiert, das es im Juni 2017 eröffnete.
In dem mehr als 3000 Quadratmeter großen Zwillingsgebäude testen zwei neue, riesige Prüfstände verschiedene Maschinenlager, indem die Ingenieure sie bewusst an die äußersten Belastungsgrenzen treiben. Der größere der beiden Prüfstände ist weltweit der erste, der ein Windenergielager mit bis zu sechs Metern Außendurchmesser in Kombination mit den Umbauteilen der Anlage testen kann. Allein dieser etwa neun Meter Breite, elf Meter hohe und acht Meter tiefe Gigant wiegt circa 700 Tonnen.
Mit ihrer millionenschweren Investition will der Konzern mit einem Jahresumsatz von gut 1,9 Milliarden Euro einerseits rätselhaften Schadensursachen auf die Schliche kommen, die – unabhängig vom Hersteller – bei Lagern mit besonders großen Dimensionen trotz akribischer Berechnungen und konstruktiver „Sicherheitsreserven“ immer mal wieder auftreten.
Gleichzeitig verfolgt SKF ein weiteres Ziel: „Die Großlager, die in Windenergieanlagen eingebaut werden, sollen möglichst zuverlässig 20 Jahre und länger laufen, sie sind also ein Schlüsselelement“, erklärt Martin Johannsmann, Vorsitzender der SKF-Geschäftsführung. Nur wenn sie reibungslos funktionierten, könne der Betreiber ein Maximum an Rentabilität erreichen. „Er hat weniger Wartungsaufwand, geringere Kosten und damit einen größeren Return on Investment.“ Obwohl SKF die Lagertechnologie schon jahrzehntelang weiterentwickelt habe, gebe es nach wie vor Optimierungspotenziale.
Es sind diese Akribie, der Wille zur Perfektion, die Innovationsbereitschaft und das Spezialwissen, die Unternehmen wie die SKF Gruppe als Zulieferer für die Offshore-Windkraft attraktiv machen. Die Boombranche bietet neben Anlagenherstellern und Servicedienstleistern auch vielen weiteren mittelständischen Unternehmen aus Süddeutschland Umsatzchancen.
Während die weißen Türme mit ihren mächtigen Rotoren meist im Norden gefertigt werden, feilen und tüfteln zahlreiche Technologiefirmen im Süden an den hochkomplexen Generatoren, Getrieben oder Lagern für die riesigen Anlagen. Allein in Bayern und Baden-Württemberg entfallen laut dem Verband Deutscher Maschinen- und Anlagenbau (VDMA) etwa 21.000 Jobs der insgesamt 143.000 direkten und indirekten Arbeitsplätze der Branche auf den Bereich Windenergie.
SKF
Knapp 500 Kilometer von der Nordsee entfernt werden im Schweinfurter Prüfzentrum von SKF Offshore-Komponenten getestet.
„In der Offshore-Windindustrie, die etwa 20.500 Beschäftigte zählt, findet sich knapp jeder achte Arbeitsplatz in Bayern und Baden-Württemberg“, erklärt Matthias Zelinger, Geschäftsführer des Fachverbands Power Systems innerhalb des VDMA.
Den Erfolg, den Unternehmen aus dem süddeutschen Raum in einer Branche erzielen, deren Aktivitäten sich an den Küsten beziehungsweise auf hoher See abspielen, führt Zelinger vor allem auf die jahrzehntelange Erfahrung der Unternehmen im Maschinenbau zurück: „Die Beschäftigung mit traditionellen Maschinenelementen ist in der Regel das Kerngeschäft der Zulieferer. Sie haben ihre Technologien erfolgreich für den Bedarf der Windindustrie weiterentwickelt.“
Dabei scheuen die bayerischen oder baden-württembergischen Unternehmen wie die 1907 gegründete SKF Gruppe weder Mühe noch Kosten: Der weltweit renommierte Technologiekonzern betreibt ein globales Netzwerk von Forschungszentren, um seinen Kunden möglichst perfekte Wälzlager, Lagereinheiten, Schmiersysteme und Dichtungen liefern zu können. Rund 6400 Mitarbeiter fertigen allein in Deutschland an zehn Produktionsstandorten kontinuierlich neue Technologien.
Wer sich dabei in der Windindustrie etabliert hat, profitiert von dem starken Wachstum des Segments: Allein von 2015 auf 2016 stiegen die Kapazitäten der weltweiten Windkraftanlagen um knapp 55 Gigawatt an Land und auf See auf insgesamt rund 487 Gigawatt – ein Plus von etwa zwölf Prozent. Und auch für 2017 prognostiziert der Weltwindenergieverband einen Zuwachs von elf Prozent. Mit einer installierten Gesamtleistung von rund 50 Gigawatt rangiert Deutschland derzeit auf Platz drei im weltweiten Ranking der Windenergieproduzenten hinter China und den USA.
Die Kompetenz der deutschen Unternehmen, speziell in der industriellen Produktion, ist nicht nur in Deutschland gefragt: Die deutschen Windenergieanlagenhersteller haben im Jahr 2015 eine Exportquote von mehr als 70 Prozent erzielt – in einem Markt, der insgesamt ein Investitionsvolumen von rund 50 Milliarden Euro umfasst. „Das eröffnet den Zulieferern gute Umsatzmöglichkeiten, zumal in diesem Gesamtmarkt das Offshore-Geschäft ein sehr langfristiges Geschäft ist“, betont VDMA-Experte Zelinger.
Die Chancen, die sich durch die Windindustrie ergeben, nutzt auch Hawe Hydraulik: Das Technologieunternehmen mit Sitz in München entwickelt und produziert Hydraulikkomponenten und -systeme für den Maschinen- und Anlagenbau und kam 2016 auf einen Umsatz von 286 Millionen Euro. Pro Jahr liefert Hawe Hydraulik zwischen 5000 und 6000 Aggregate für Offshore-Windkraftanlagen weltweit aus.
„Bis 1999 haben wir nur Komponenten für Windkraftanlagen produziert“, erzählt Andreas Nocker. Ab diesem Zeitpunkt habe Hawe Hydraulik dann komplette Aggregate entwickelt und gefertigt, ergänzt der Manager, der den Bereich erneuerbare Energien verantwortet. Die etwa 80 Kilo schweren und 70 Zentimeter großen Geräte stellen den Druck her, den eine Windkraftanlage benötigt, um die hydraulisch betriebenen Komponenten wie die Bremsen, den Servicekran oder die Rotorverriegelung zu steuern.
Hawe Hydraulik
Andreas Nocker ist beim Münchner Mittelständler Hawe Hydraulik für den Bereich erneuerbare Energien zuständig.
„Unser CEO Karl Haeusgen hat mit dieser Entscheidung viel Weitsicht bewiesen“, betont Nocker. Denn so war Hawe Hydraulik optimal aufgestellt, als der Offshore-Markt weltweit an Dynamik gewann.
Seit 2001 produziert das Unternehmen Aggregate für einen spanischen Windkraftanlagenhersteller. Auch in Dänemark und Deutschland setzt Hawe Hydraulik inzwischen eine Vielzahl an Geräten ab. „Seit 2006/07 sind wir in China vertreten. Hier beliefern wir einen der fünf größten Windkraftanlagenbauer des Landes – und in China wächst der Offshore-Markt rasant“, sagt Nocker.
„Wer bei einem Anlagenhersteller als Zulieferer mitmischen will, muss quasi von Anfang mit dabei sein“, erklärt der Hawe-Manager. Ansonsten sei es schwierig, in dem Markt Fuß zu fassen. Der Grund: Die Aggregate, wie sie beispielsweise Hawe Hydraulik anbietet, kosten zwischen 2000 und 4000 Euro – eine Kleinigkeit im Verhältnis zu den Gesamtkosten einer Anlage von 1,5 bis zwei Millionen Euro.
„Passt dann die Qualität des Produkts, sehen die Hersteller keinen Grund, den Zulieferer zu wechseln“, schildert Nocker die übliche Praxis der Windkraftanlagenbauer. Einstiegschancen ergäben sich eigentlich nur dann, wenn neue Windparks entstünden oder ein Konkurrent nicht die gewünschte Qualität liefere.
„Die Laufzeit einer Windkraftanlage ist auf 20 Jahre ausgelegt, und so lange sollte natürlich auch das Aggregat halten“, erklärt Nocker. Um den extremen Klimabedingungen und der salzhaltigen Luft auf See standzuhalten, fertigt Hawe Hydraulik seine Geräte komplett aus Stahl. „Der Oberflächenschutz ist hier natürlich ebenso ein Thema wie die Leistungskapazität des Geräts“, zählt Nocker die kritischen Punkte auf, die die Qualität eines Aggregats ausmachen.
In der Regel benötige ein Windrad einen Druck von 200 bis 250 Bar, um die verschiedenen Komponenten steuern zu können. „Wir legen unsere Aggregate von Haus aus größer aus – bis zu 400 Bar. So stellen wir sicher, dass das System nicht nur 20 Jahre lang unter größter Belastung arbeitet, sondern absolut zuverlässig seine Leistung bringt.“
Für Hawe Hydraulik besteht die nächste Herausforderung vor allem darin, für die kommenden Generationen der Windparks passende Aggregate zu entwickeln. „Die Anlagen werden immer leistungsfähiger. Statt Zwei- bis Drei-Megawatt-Anlagen entstehen inzwischen Sechs-Megawatt-Anlagen – und eine Anlage mit 9,5 Megawatt ist bereits in Planung“, sagt Nocker.
Auch dank dieses technologischen Fortschritts blickt SKF-Konzernchef Alrik Danielson optimistisch in die Zukunft, allen Diskussionen um das gebremste Tempo in der Offshore-Windkraft zu Trotz: „Es mag sein, dass der Ausbau der erneuerbaren Energien in Deutschland derzeit ein wenig stockt. International gesehen glauben wir fest an das Geschäft mit der Windkraft“, erklärt er.
Da die Anlagen immer leistungsfähiger würden, stiegen die Ansprüche an die Herzstücke der Windräder. „Insofern ist die SFK-Investition in das neue Prüfzentrum so etwas wie eine Wette darauf, dass sich die weltweite Windenergieindustrie auch in Zukunft positiv weiterentwickeln wird.“