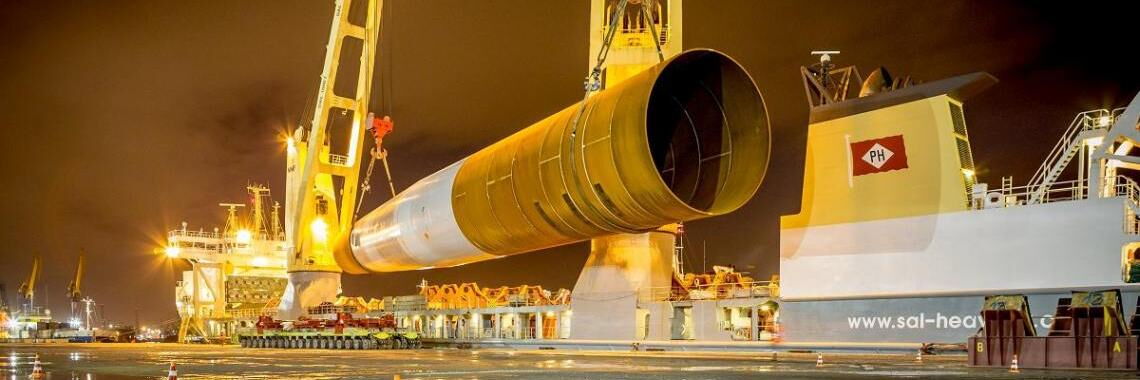
Sal Heavy LIft
Verschiffung von Offshore-Wind-Fundamenten
Sal Heavy LIft
Von Hans Wille
Der Regen peitscht den beiden Männern ins Gesicht. Mit zugezogener Kapuze besteigen sie eine hydraulische Arbeitsbühne und schrauben sich damit entlang einer mächtigen signalgelben Stahlsäule in die Höhe. Immer weiter geht es hinauf, fünf Meter, zehn Meter, 20 Meter. Ganz oben wechseln sie schließlich von der Hebebühne auf eine Plattform, die an der Stahlsäule angeschweißt ist.
Sie stehen jetzt 30 Meter über dem Hafen des dänischen Aalborg auf einem sogenannten Transition Piece – einem zentralen Bauteil von Offshore-Windrädern. Es soll später einmal in der Irischen See über ein 80 Meter langes Fundament gestülpt werden, das zuvor im Meeresboden verankert wurde. Anschließend wird auf dem Transition Piece der Turm befestigt, ganz oben folgen das Maschinenhaus von der Größe eines Linienbusses und die riesigen Rotorblätter des Windrads.
Beim Bau eines Offshore-Windparks geht es fast immer um solch gewaltige Dimensionen – um Stahlelemente, die Hunderte Tonnen wiegen und Kirchtürme überragen, um präzise Arbeit im Angesicht der Elemente und hohe Ingenieurskunst.
Wie jetzt am Hafen von Aalborg, wo Energie-Winde live bei der Verladung der letzten sechs von 87 Transition Pieces für den Offshore-Windpark Walney Extension vor der Nordwestküste Englands dabei ist. Es ist ein beeindruckendes Beispiel der Leistungsfähigkeit dieser noch jungen Industrie.
Oben auf der Plattform werden die beiden Männer im peitschenden Regen nun das 530 Tonnen schwere Bauteil an das eigens gefertigte Lifting-Tool anschlagen, das ein paar Meter höher am Bordkran der „MV Svenja“ hängt. Sie ist das Flaggschiff von SAL Heavy Lift, einer der führenden Schwergutreedereien der Welt.
Henning Kaschke, der Zweite Offizier der „Svenja“, dirigiert per Sprechfunk den Bordkran, damit das Tool an zwei dafür gedachten Vorrichtungen des Transition Pieces befestigt werden kann, in der Fachsprache Lifting-Augen genannt.
Zentimeter für Zentimeter senkt Jorge Malapote, der philippinische Fahrer von Bordkran zwei, das Tool. Zwischendurch dirigiert Kaschke es etwas nach links und zugleich wenige Grad gegen den Uhrzeigersinn, bis sich das eine der beiden u-förmigen Enden des Tools wenige Zentimeter über den angeschrägten Rand des einen Auges stülpt.
Sal Heavy LIft
Das Tool ist leicht schräg aufhängt, damit nicht beide Augen gleichzeitig eingefädelt werden müssen. Für das andere Auge fehlen noch gut zehn Zentimeter Höhe und ein letzter seitlicher Dreh des Tools. Dafür greift ein zweiter Mann das Tauende, das an dem Lifting-Tool baumelt, und zieht das zwölf Tonnen schwere Gerät fast mühelos in seine exakte Position senkrecht über dem Auge.
„Hook down!“, ruft Kaschke in sein Mikro, das Tool setzt sich nun auch über den Ansatz des zweiten Auges. „Stopp!“
Jetzt richten die Männer mit den groben Arbeitshandschuhen das Innere der beiden Augen, einen kugelgelagerten Ring mit dem Außendurchmesser eines Handballs, so aus, dass er senkrecht steht. „Hook down!“, sagt Henning Kaschke erneut, und das Tool setzt sich über die beiden Augen. Eine Hydraulik schiebt armdicke Bolzen durch die u-förmigen Halterungen und die dazwischen sitzenden Augen: Das Transition Piece ist angeschlagen.
Wer die präzise Arbeit beobachtet und sich die Dimensionen des Projekts bewusst macht, versteht, was Peter Rom Poulsen meint, wenn er sagt, dass Offshore-Windparks zu den größten Infrastrukturvorhaben in Europa gehören. Poulsen ist als Projektleiter beim dänischen Energiekonzern Ørsted für den Windpark Walney Extension verantwortlich und damit letztlich der Auftraggeber der Verladung.
„Wegen der komplexen logistischen Herausforderungen ist die Zusammenarbeit mit unseren Partnern und Zulieferern enorm wichtig, um den reibungslosen und sicheren Bau unserer Windfarmen zu gewährleisten“, sagt er.
Sal Heavy LIft
Bis hierher hat die Aktion hat rund sechs Minuten gedauert. Mit zwei entsprechend großen Schraubbolzen anstelle des Lifting-Tools wäre sie auch möglich gewesen, hätte aber rund eine halbe Stunde gedauert. Hochgerechnet auf 87 Transition Pieces, die beim Be- und beim Entladen jeweils an- und abgeschlagen werden, bedeutet das eine Nettozeitersparnis von gut 140 Stunden oder knapp sechs Tagen.
„Da rechnet sich der Bau des Tools, obwohl es rund 150.000 Euro gekostet hat“, erläutert SAL-Chefingenieur Karsten Behrens.
Fast fünf Monate hat der Ingenieur mit seinem Team den kompletten Verladevorgang durchdacht, geplant, berechnet. „Natürlich sind auch die Praktiker von der Brücke an dem theoretischen Prozess beteiligt. „Schließlich kennen die Nautiker das Schiff in all seinen Details und wissen, wo die ‚Svenja‘ besonders sensibel reagiert.“
Nun beginnt der eigentliche Verladevorgang der 530 Tonnen gelb lackierten Stahls. Aber nicht so, wie ein Laie sich das vorstellen mag: Würde Kranführer Jorge Malapote das armdicke Stahlseil jetzt unter Zug setzen, würde das Gewicht, das neben dem Schiff am Kran hinge, die „Svenja“ in kürzester Zeit zum Kentern bringen.
„Die Lastverteilung ist das A und O beim Heavy-Lifting“, sagt Kapitän Matthias Pfeiffer: „In jedem Moment des Verladens muss das Schiff satt und sicher auf dem Wasser liegen.“
Sal Heavy LIft
Der Kapitän steht mit Blick zum Heck auf der Brücke. Von hier aus schaut er in den gähnend leeren Laderaum, lang und tief wie die Baugrube einer U-Bahn-Haltestelle. Rechts daneben, auf der Backbord-Galerie, stehen hintereinander die beiden bordeigenen Kräne, und noch weiter rechts, im Hafen, die sechs Transition Pieces.
Für das Laden sind beide Kräne besetzt. Kran eins arbeitet mit seinem Ausleger als Gegengewicht, während Kran zwei für das Laden zuständig ist. Um die Stabilität zu gewährleisten, beordert Pfeiffer zunächst den Ausleger des ungenutzten Krans eins über das Schiff hinweg gen Steuerbord. In dem Tempo, in dem der zwölf Tonnen schwere Ausleger von der Seite der Kaikante auf die Seeseite des Schiffes dreht, kann der Kapitän auf einem Display beobachten, wie ein schwarzer Balken aus der Mitte einer waagerechten Linie, dem Nullpunkt, nach links zur Seeseite auswandert.
Der Balken bleibt bei 1,8 stehen; das Schiff hat sich um 1,8 Grad nach Steuerbord geneigt, allein durch das Eigengewicht des unbelasteten Krans. Zudem ist auf der Wasserseite ein Stabilitätsponton angedockt, ein luftgefüllter Schwimmkörper, der mehrere Meter entfernt starr mit dem Schiff verbunden ist und den Querschnitt des Schiffes und damit seine Stabilität vergrößert.
„Jede Neigung von weniger als zwei Grad ist kein Problem. Ab drei Grad könnte ich nervös werden“, sagt Pfeiffer. „Hook up!“, ordnet der Kapitän an.
Sal Heavy LIft
Langsam setzt Kranführer Malapote das Seil in Bewegung, an dem das Transition Piece angeschlagen ist. Der Kapitän sieht auf dem Display, wie die Neigung des Schiffes sich langsam gen null bewegt. Das zeigt, dass der Kran schon ein Gutteil der 530 Tonnen am Haken hat, obwohl das Element noch am Boden steht.
Jetzt setzt der Kapitän zusätzlich die drei Ballastwasserpumpen in Gang, zusammen bewegen sie 25 Kubikmeter Wasser pro Minute von Back- nach Steuerbord, wodurch der schwarze Neigungsbalken sichtlich langsamer Richtung null Grad wandert.
Im Idealfall verliert der Stahlkoloss in dem Moment den Bodenkontakt, in dem der Neigungswinkel des Schiffes null Grad beträgt. „Dann hebt sich der Fuß des Transition Pieces parallel vom Boden ab, es ergibt sich also kein Spalt unter einer Seite des Stahlrohrs, während das Gegenüber noch auf dem Boden steht. Sonst würde es unweigerlich am Haken schaukeln.“
Der Dritte Offizier Henrik Bahnsen beobachtet an der Kaikante, wie sich der erste Spalt zwischen der Stahlsäule und den massiven Holzklötzen bildet, auf denen es ruht. „Shore-side comes up!“, funkt er zum Kapitän. Dann hängt das ganze Rohr frei in der Luft. Und pendelt kurz ein wenig hin und her.
Kranführer Jorge Malapote hat in der kleinen Krankanzel mit Glasboden einen noch besseren Überblick als der Kapitän. Bevor er jedoch die Last an Bord heben kann, ballastet der Kapitän das Schiff gegenläufig zum Vorgang von vor wenigen Minuten. Da das Transition Piece von Backbord in die Mittschiffslinie bewegt werden soll, beordert er den Ausleger des unbelasteten Krans eins zurück nach Backbord.
Das Display zeigt unverzüglich die Gewichtsverschiebung an: Der schwarze Balken schlägt um 1,2 Grad nach Backbord aus. Außerdem pumpt er das Ballastwasser zurück nach Backbord. Zeitgleich gibt er Kranfahrer Malapote das Go. Der hebt das Transition Piece so hoch, dass es über dem Deck schwebt, anschließend dreht er es im Zeitlupentempo zum Schiff.
Die Idee: Der langsame Effekt des Pumpens egalisiert den etwas schnelleren Effekt des Lastendrehens auf das Schiff so, dass die Neigung am Ende bei null Grad liegt. Tatsächlich wandert der schwarze Balken auf dem Display tendenziell nach links. Als das Transition Piece genau über der Mittschiffslinie schwebt, hat das Schiff noch etwas Neigung nach Steuerbord. Deshalb wartet der Kapitän, bis er die Ballastwasserpumpen ausstellt.
Dann erst kann das Monstrum in eine Position senkrecht über seinem Platz auf der Stahlkonstruktion im Laderaum dirigiert werden, auf der alle sechs Transition Pieces während der Seereise befestigt werden. Auch diese Tragekonstruktion aus 180 Tonnen Stahl ist eine Spezialanfertigung. „Eine Lösung von der Stange haben wir nur selten“, sagt Chefingenieur Behrens.
Etwas später setzt das Rohr exakt am vorgesehenen Platz auf. Die philippinische Crew beginnt sofort mit dem Festlaschen, wobei sie unter anderem massive Stahlklammern von den Ausmaßen eines doppelten Ziegelsteins einsetzen. Dann endlich ist das erste Transition Piece transportbereit.
Für all sechs Stahlkolosse braucht das Team rund 7,5 Stunden. Schließlich ist es geschafft, die „Svenja“ kann zu ihrer Fahrt nach Belfast aufbrechen. Es ist die 29. und letzte Verschiffung von Aalborg aus. Zwischendurch hat die Reederei auch die 80 Meter langen Monopiles für Walney aus Rostock transportiert. Alles geschieht nach einem ausgeklügelten Plan, sodass die Arbeiten an dem Offshore-Windpark nicht ins Stocken geraten.
Der Auftraggeber ist zufrieden. Ørsted-Projektleiter Poulsen sagt: „Die Teams, mit denen wir zusammenarbeiten, kennen die Herausforderung und wissen was wir von unseren Partnern erwarten.“
In Aalborg ist es schließlich so weit: Noch einmal legt das Schiff ab und verlässt den dänischen Limfjord. Mit den sechs gelben Säulen an Bord sieht es ein bisschen aus wie die Kinderzeichnung eines alten Dampfschiffs.